La dureza o el concepto de dureza tiene un determinante importante y definitorio en el campo de la Tribología y con más enfoque en el de la Terología. En el imaginario común existe el axioma de que a más dureza de un material o de un recubrimiento, mayor protección contra fenómenos de desgaste como abrasión, erosión, etc.
Este pensamiento no es del todo errado, es más, muchos recubrimientos del mercado son definidos por el valor de dureza que este posee. Incluso la clasificación o su designación trae implícito la dureza usualmente en HRC (Rockwell C) del producto aplicado.
Entendemos la dureza como la propiedad de un material (ya sea por constitución o por una capa de recubrimiento) de impedir que otro material lo penetre, lo raye, lo desgaste. Así, se han generado diferentes métodos de medición de la dureza que, básicamente, dependen del material o del recubrimiento que se desea identificar.
Existen desde polímeros y plásticos que su medida es en escala Shore, hasta materiales ferrosos y no ferrosos que cuentan con escalas de dureza en unidades de Rockwell B, C, vickers, Brinell, etc. Todas estas van definidas por la forma de indentación, la técnica de medición, los materiales para este y el proceso de lectura de la huella que deja el proceso de penetración de la herramienta cuantificadora.
El inconveniente radica cuando establecemos la dureza que la ficha técnica o el fabricante nos da como único parámetro importante para un buen recubrimiento.
La efectividad de un recubrimiento recae en una variedad de parámetros y disposiciones, no solo en su dureza al final de la aplicación.
Los diferentes aleantes que componen el recubrimiento, su disposición metalográfica, densidad o posicionamiento en el volumen del material aplicado, el proceso de fabricación, la disposición térmica, la dilución, el tipo de fenómeno de ataque, el tipo de material incidente o atacante y muchos otros conceptos definen el rendimiento y la real protección ante los fenómenos de desgaste.
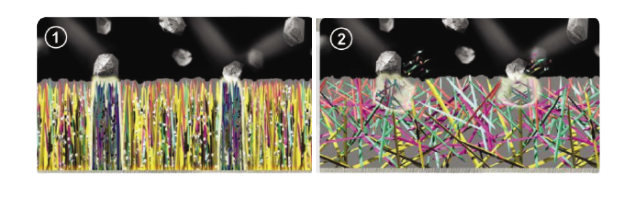
Una aplicación o aleante común es el carbón. Se ha utilizado como aleante para recubrimientos protectores, incluso en procesos de tratamiento térmico, donde se busca la distribución de los aleantes constituyentes y de la interacción con este elemento para generar protección por medio de durezas superiores a la de los materiales madres.
Los carburos de cromo en materiales con proporciones significativas de Cr por ejemplo, son otro de los tantos constituyentes que predominan en las propiedades de algunos recubrimientos protectores. Generan una dureza alta, la cual desembocaría en una protección determinada, o así lo sustentaríamos. Pero los carburos de cromo constan de 3 formas de estructura cristalina, que con el mismo valor de dureza pueden generar diferentes calidades de protección.
Otro ejemplo es la distribución de los constituyentes. Como se puede observar en la imagen previa, la forma y agrupación de los carburos de la índole que sea (elementos unidos con el carbón), puede generar para una misma dureza diferentes características de protección.
Lo importante en la selección del tipo de recubrimiento a utilizar es un análisis adecuado de los factores generadores del desgaste; materiales, actividad, medio circundante, etc.
De esta manera podremos seleccionar el tipo de material ya sea polímeros, soldadura, procesos de metalización y demás, con sus respectivos aleantes, adecuados para combatir los desgastes presentes.
Continuaremos analizando algunos materiales, como lo son aceros especiales de alto desempeño, aleantes en soldadura más comunes y procesos de alta tecnología. Enfocados en su uso y pertinencia de la utilización de los mismos en la protección de nuestros elementos de máquinas.
No olvides seguirnos en Facebook, Instagram, LinkedIn y YouTube. En estos canales también compartimos información valiosa y tips para la industria metalmecánica en general.