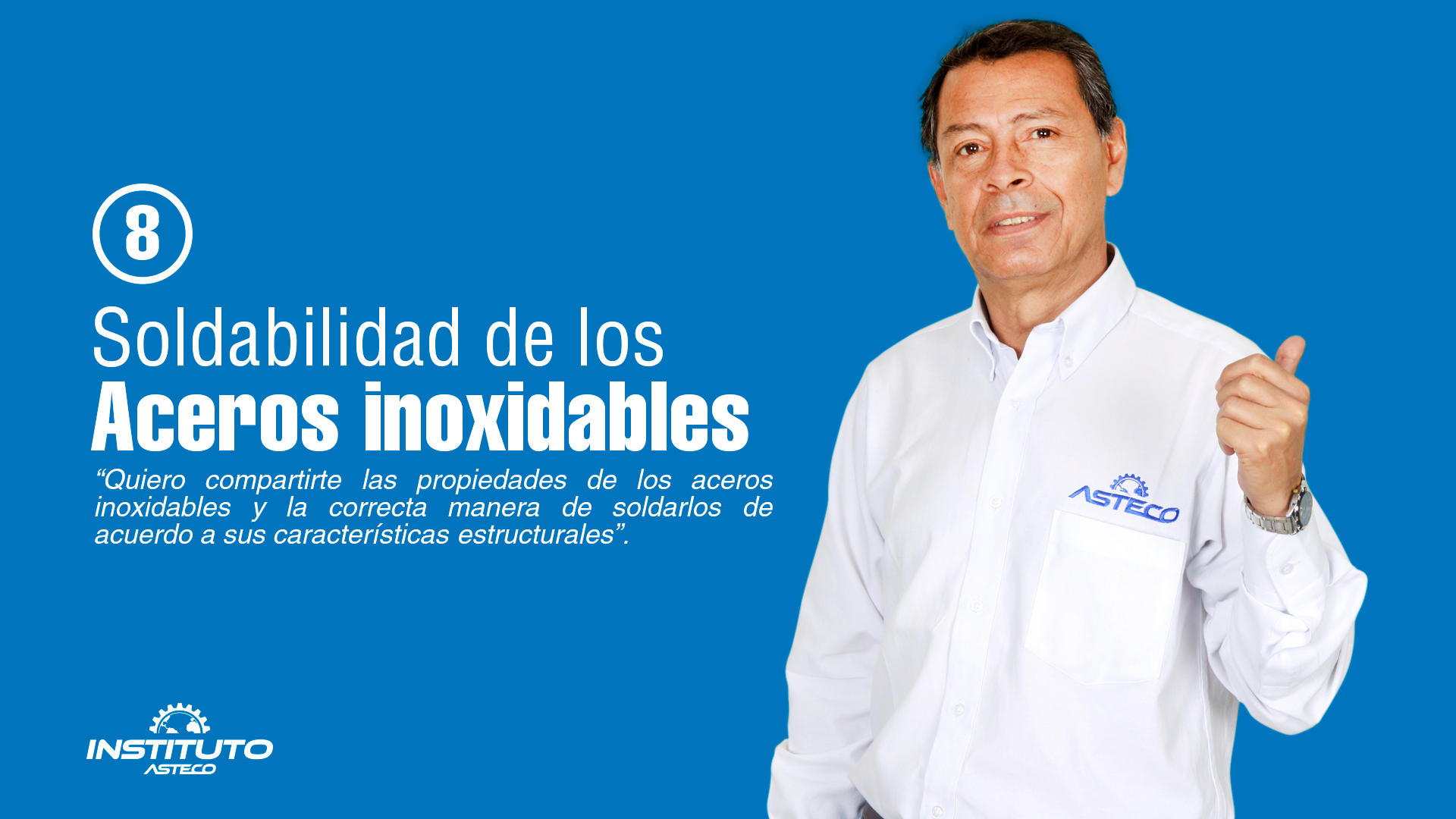
Introducción
Al finalizar este curso conocerás la clasificación de los aceros inoxidables y los electrodos utilizados para su soldadura.
También te compartiré las recomendaciones que debes tener en cuenta para soldar cada una de las diferentes series de aceros inoxidables, sin alterar sus propiedades.
Comprenderás el proceso químico generado con el decapado y pasivado del acero inoxidable, así como la correcta manera de aplicarlos.
Y podrás comparar los diferentes electrodos usados en la soldadura de acero inoxidable, sus propiedades y la correcta aplicación en cada caso, de acuerdo a tus necesidades
Historia
En 1913, el Metalurgista inglés, Harry Bradley, al investigar muestras de forros de cañón de acero de alto Cromo, observó a través del microscopio su resistencia a diversos medios ácidos. Intuyendo un descubrimiento significativo, estudió la corrosión que brinda el Cromo a los aceros.
Los aceros inoxidables son aleaciones con base en hierro que contienen al menos un 11% de Cromo distribuido uniformemente a través del material.
La adición de Cromo en presencia de oxígeno forma una película de óxido de Cromo Cr203 en la superficie del acero, que genera resistencia a la corrosión.
Su aplicación se encuentra en cualquier tipo de industria, especialmente de alimentos, petroquímica, aviación, textil, química, papelera, hospitalaria, industria médica, etc. Algunas piezas fabricadas en aceros inoxidables son:
Cilindros – containers – tubos – ejes – engranajes y carcasas.
Aceros inoxidables
Los aceros inoxidables más comerciales han sido clasificados por el Instituto Americano del Hierro y del Acero (AISI) bajo un sistema de numeración de tres dígitos. Los dos últimos números no tienen un significado específico, pero el primero indica el grupo al cual pertenece. Así:
- Serie 2XX Cromo-Niquel-Manganeso; Austeníticos, No Magnéticos, No Templables.
- Serie 3XX Cromo-Niquel; Austeníticos, No Magnéticos, No Templables.
- Serie 4XX Al Cromo; Martensíticos, Magnéticos, Templables.
- Serie 4XX Al Cromo; Ferríticos, Magnéticos, No Templables.
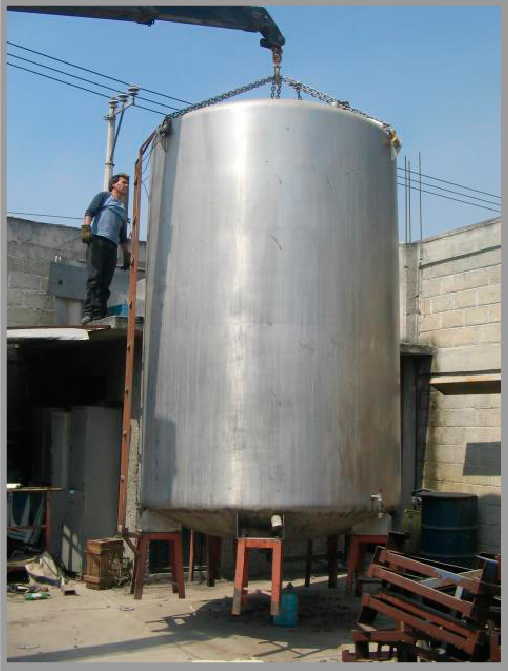
Composición química de algunos aceros inoxidables
AISI | C | Mn | Si | Cr | Ni | P | S | Mo |
---|---|---|---|---|---|---|---|---|
304 | 0.08 | 2.0 | 1.0 | 18 | 8 | 0.04 | 0.04 | |
304L | 0.03 | 2.0 | 1.0 | 18 | 10 | 0.04 | 0.04 | |
308 | 0.08 | 2.0 | 1.0 | 20 | 11 | 0.04 | 0.04 | |
309 | 0.15 | 2.0 | 1.0 | 23 | 13.5 | 0.04 | 0.04 | |
310 | 0.15 | 2.0 | 1.0 | 25 | 20 | 0.04 | 0.04 | |
316 | 0.08 | 2.0 | 1.0 | 17 | 12 | 0.04 | 0.04 | 2.0 |
316L | 0.03 | 2.0 | 1.0 | 17.5 | 12.5 | 0.04 | 0.04 | 2.4 |
0.13 | 2.0 | 1.0 | 12 | 2.0 | 0.04 | 0.04 | ||
420 | 0.32 | 2.0 | 1.0 | 13 | 0.04 | 0.04 | ||
430 | 0.1 | 1.0 | 1.0 | 16 | 0.04 | 0.04 |
Cuadro comparativo de la resistencia a la corrosión intergranular
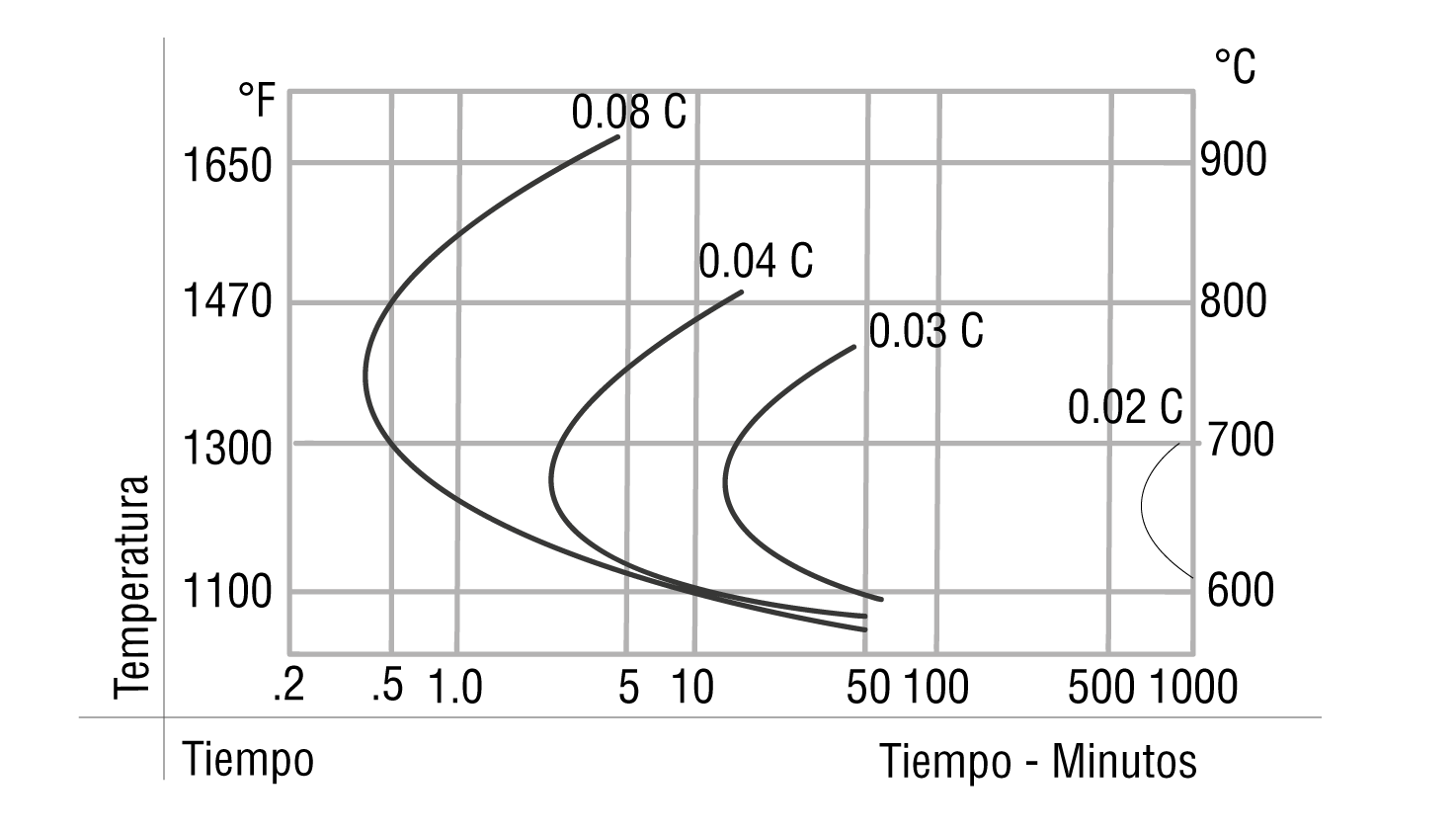
Relación tiempo-temperatura para producir susceptibilidad a la corrosión intergranular en un acero 304 con varios contenidos de Carbono
Clasificación
Clasificación de electrodos inoxidables AWS A5.4-95
Designación de los electrodos para aceros inoxidables
E-XXX-XX
- E Indica que es un electrodo para proceso de soldadura de arco manual (SMAW).
- XXX Los tres dígitos siguientes, indican el tipo de aleación, similar a la ultilizada en la clasificación de los aceros inoxidables.
- XX Los dos últimos dígitos indican: el primero, las posiciones en que se puede soldar, 1 significa todas las posiciones; el segundo número indica el tipo de recubrimiento del electrodo y según esto, el tipo de corriente. Así, por ejemplo, 5 indica que solo debe usarse corriente continua y polaridad al positivo. 6, que se puede usar con corriente alterna o directa y electrodo al positivo.
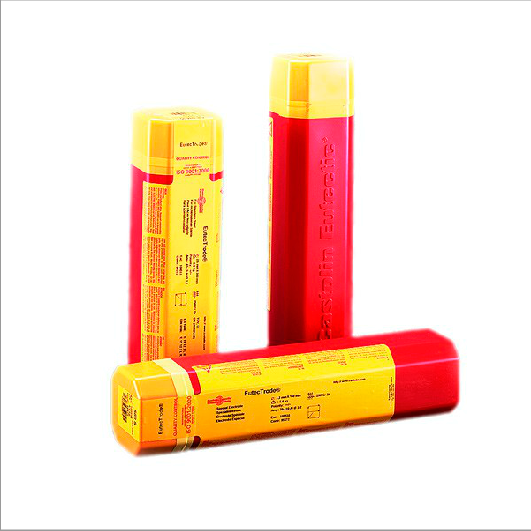
Electrodos inoxidables
Fabricación del revestimiento
- Para la fabricación del revestimiento se suelen utilizar hasta 40 minerales y sustancias distintas. La selección, origen y dosificación de cada componente que va a intervenir en la composición del revestimiento es un secreto celosamente guardado por el fabricante.
- La composición del revestimiento suele ser muy compleja. Se trata generalmente de una serie de sustancias orgánicas y minerales.
- En la fabricación de la pasta para el revestimiento suelen intervenir: calcio o minerales alcalinos térreos y elementos ionizantes tales como el Potasio, que estabilizan el arco, permitiendo el uso de corriente alterna.
- Óxido de Titanio + óxido de Silicio para todas las posiciones, ideal para posición plana.
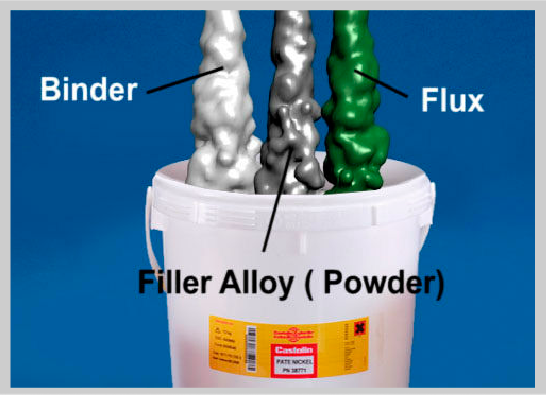
Recomendaciones
Soldabilidad de los aceros inoxidables serie 300
- No precaliente los aceros inoxidables SERIE 300.
- Use electrodos del menor diámetro posible.
- Fije el amperaje lo más bajo posible.
- Utilice un arco corto y sin oscilar el electrodo.
- Llene todos los cráteres, dé un enfriamiento rápido.
- La selección del electrodo debe ser igual al metal base.
- Mantenga los electrodos sin humedad.
- Mantenga la temperatura por debajo de 300°C.
- Use solo escobillas de acero inoxidable.
- Al soldar con electrodos revestidos queda una capa de coloración negruzca o verdosa debido al uso de fundentes de la película protectora, esta es altamente corrosiva y debe ser removida antes de poner la parte en servicio. Los revestimientos y los fundentes contienen fluoruros de Calcio, Sodio y Potasio que ayudan a retirar la capa de óxido de Cromo de la superficie a soldar.

Soldabilidad de los aceros inoxidables serie 400 Martensíticos
- Precaliente los aceros inoxidables SERIE 400 a temperatura de 100°C - 150°C
- Seque los electrodos a 300°C por 2 horas a 250°C de 4 a 6 horas.
- Use electrodos del menor diámetro posible.
- Fije el amperaje lo más bajo posible.
- Utilice un arco corto y sin oscilar el electrodo.
- La selección del electrodo debe ser igual al metal base, o que el aporte supere las condiciones del trabajo.
- Mantenga los electrodos sin humedad.
- Mantenga la temperatura de interpase a 150°C.
- Use sólo escobillas de acero inoxidable.
- Al soldar con electrodos revestidos verifique la sanidad del déposito de soldadura, limpiando con herramienta de corte (fresa) o grata de acero inoxidable.
- Realice alivio de tensiones a temperatura de 570°C a 600°C durante una hora por cada pulgada de espesor.
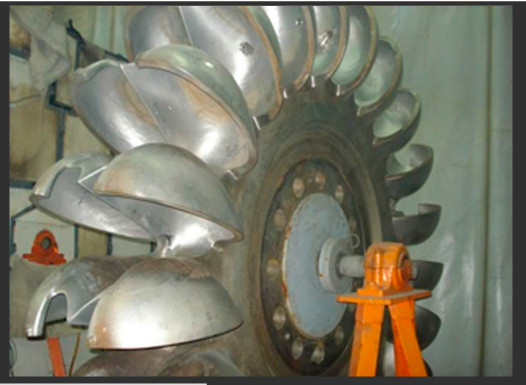
Diagrama de SCHAEFFLER
Antón Schaeffler estudió el efecto en la microestructura de los principales elementos de los aceros inoxidables y construyó su conocido "Diagrama de Schaeffler", el cual predice la microestructura de depósitos de acero inoxidable con base en su composición química.
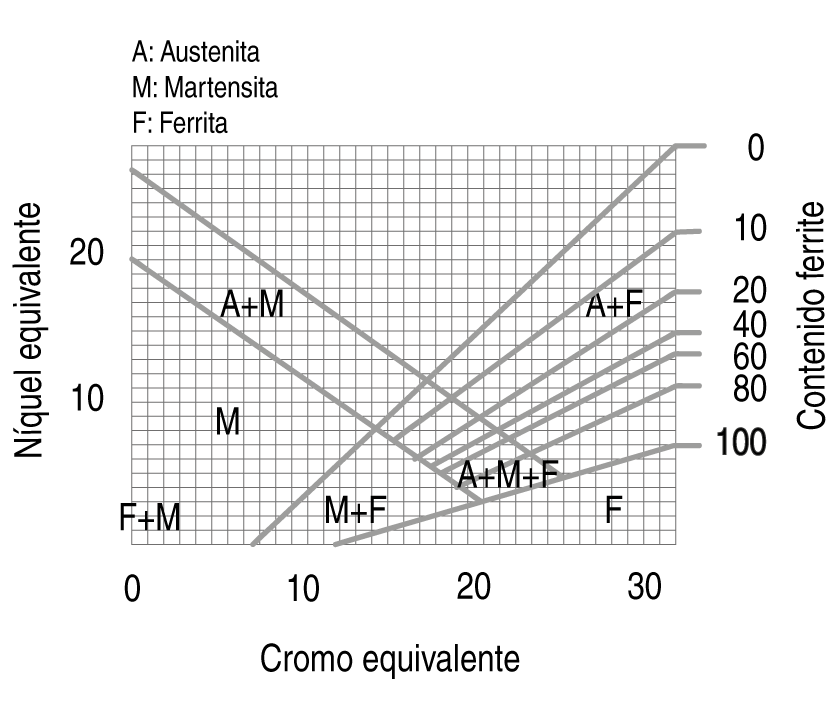
Decapado y pasivado de aceros inoxidables
- El decapado: es un ataque químico sobre la superficie de los materiales para eliminar
óxidos, trazas de hierro y suciedad en general. El baño de decapado tiene una composición apropiada para
no dañar al acero inoxidable.
El baño típico de decapado está compuesto de: 20-30% ácido nítrico +3-6% ácido fluorhídrico, y el resto agua. Para acelerar, se calienta entre 40 y 50°C. - El pasivado: es un ataque químico sobre la superficie de los materiales para
conseguir que se formen los "óxidos buenos", que son los óxidos protectores.
En el caso del acero inoxidable es el óxido de cromo.
El baño típico del pasivado está compuesto de: 25-35% de ácido nítrico, el resto de agua. Se suele utilizar a temperatura ambiente.
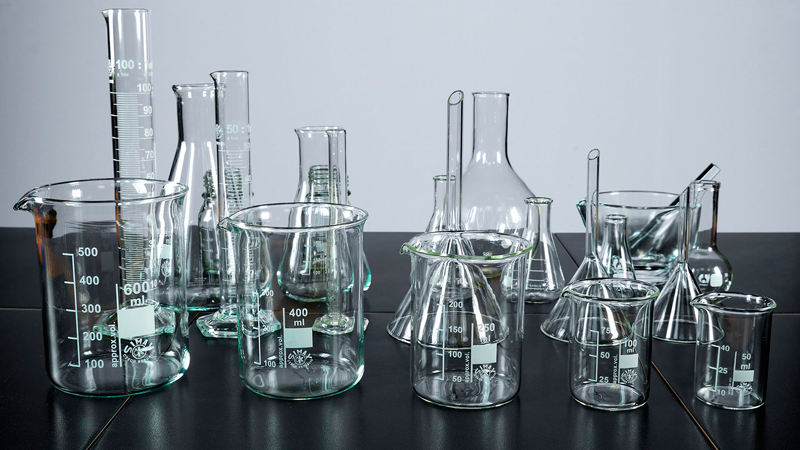
Electrodos
Eutectrode 52 NG
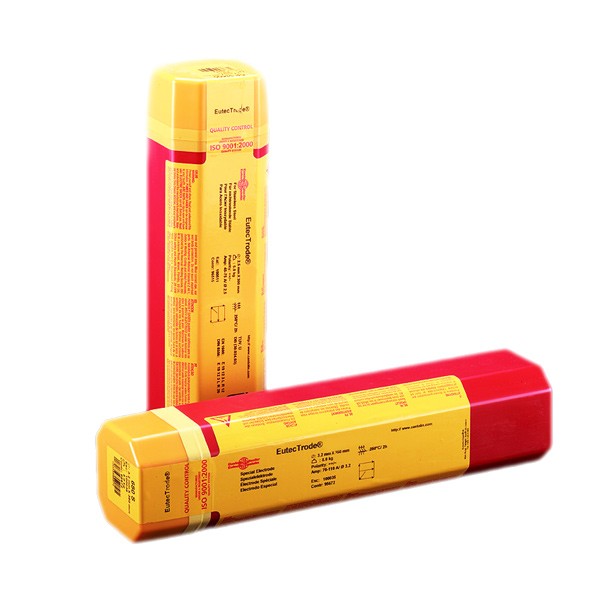
Electrodo de nueva generación que ofrece mayor velocidad de depósito y aplicación a menores amperajes. Muy buena resistencia a la oxidación a altas temperaturas, trabaja en toda posición, para soldar aceros inox. tipo 310, 314, 403, 430, y 440.
Usado para unión y reconstrucción de aceros inoxidables del tipo 25/20, recubrimientos resistentes a altas temperaturas, unión de aceros inoxidables de composición desconocida. Intercambiadores de calor, excelente para la unión de anclajes de hornos en la industria cementera, etc.
Resistencia a la tracción: 85.000 PSI
Alargamiento: 30-35%
Dureza: 160 HB
Eutectrode 53L NG
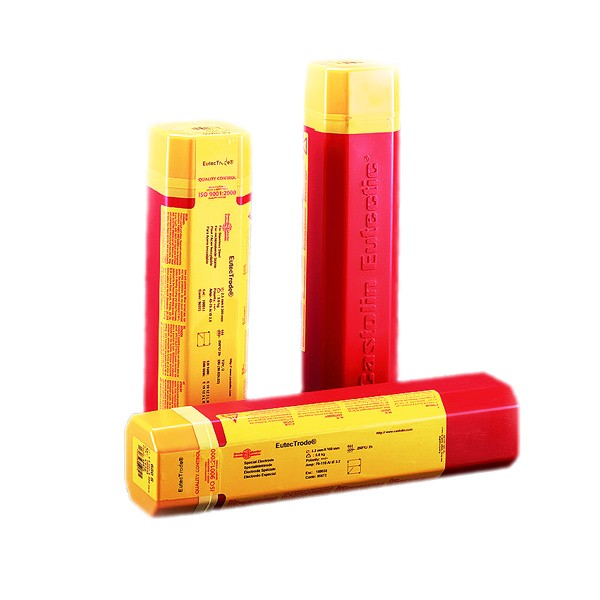
Electrodo de contacto que proporciona al operario mayor control sobre el charco de soldadura y un menor calentamiento, excelente resistencia a la corrosión intergranular, aplicable en toda posición, para soldar aceros inoxidable Tipo 316L, electrodo con bajo contenido de carbono.
Usado para la fabricación, reconstrucción y mantenimiento de elementos en la industria química y de alimentos (bombas, tanques, tuberías, agitadores, digestores), como recubrimiento donde se necesita mediana dureza y una excelente resistencia a la corrosión
Resistencia a la tracción: 85.000 PSI
Alargamiento: 30-35%
Dureza: 170 HB
Eutectrode 54L NG

Electrodo que ofrece un menor aporte térmico y menor distorsión del metal base, excelente resistencia a la corrosión intergranular, aplicable en toda posición, fácil remoción de escoria, para soldar aceros inox.
Usado para uniones de aceros inoxidables tipo 304, 304L, 308, 308L, fabricación, reconstrucción de elementos en general, cocinas integrales, cantinas lecheras, lavadoras industriales, bombas, tanques agitadores, etc.
Resistencia a la tracción: 80.000 PSI
Límite elástico: 58.000 PSI
Alargamiento: 35%
Dureza: 190 HB
Eutectrode 57L NG
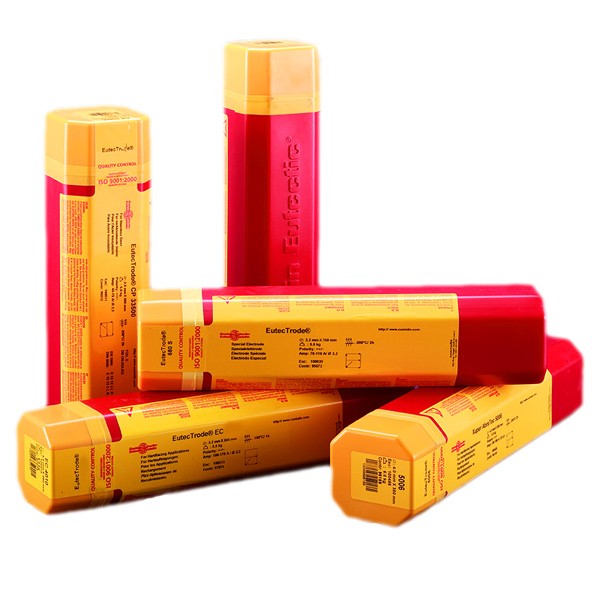
Electrodo especial para la unión de aceros al carbón con aceros inoxidables, buena maquinabilidad, aplicable en toda posición, resistente a la fisuración en caliente, resistente a la oxidación en caliente hasta 1.100°C.
Usado para la unión de acero inox con acero carbono, recubrimientos sobre aceros al carbono, unión de aceros difíciles de soldar de los tipos Cr, Cr-Ni, Ni-Mo, intercambiadores de calor, etc.
Resistencia a la tracción: 90.000 PSI
Límite elástico: 58.000 PSI
Alargamiento: 30-35%
Electrodos
Eutectic 4902
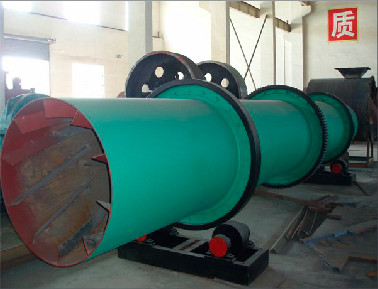
Electrodo para soldar aceros tipo 307, presenta buena resistencia al agrietamiento, corrosión y la tracción. Excelente resistencia a la oxidación y al calor, posee buena maquinabilidad.
Usado para uniones y revestimientos tenaces con alta resistencia al desgaste.
Resistencia a la tracción: 90.000 PSI
Alargamiento: 45-50%
Dureza: 200 HB
Eutectic Xuper 4709
Electrodo con buena resistencia a la fricción, corrosión, al agrietamiento y altas temperaturas, aplicable en toda posición, buena maquinabilidad.
Usado para la unión de aceros al carbono con aceros inoxidables; especialmente para juntas en aceros inoxidables tipo 309, muy apropiado para ambientes a temperaturas de 1000°C.
Resistencia a la tracción: 80.000 PSI
Alargamiento: 30-35%
Dureza: 200 HB
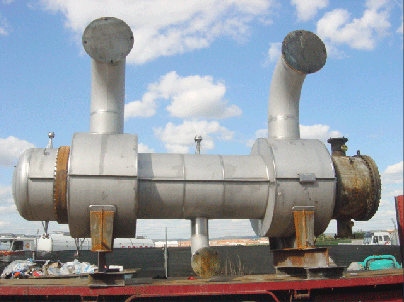
MG 698(AWS A5.4 E410 NiMo-15)
- Mg 698 ha sido desarrollado para la soldadura de aceros forjados y fundidos con composición similar a un acero ASTM CA6NM y fundiciones tipo 410, 410S y 405. El depósito es un Cromo-Niquel para un óptimo desempeño.
- Usado para soldaduras en aceros inoxidables martensíticos para juntas y recargues en áreas sujetas a corrosión, cavitación-erosión. Típicas aplicaciones incluyen turbinas hidráulicas, bombas y cuerpos de válvula, etc.
- Resistencia a la tensión: mínimo 110.000 PSI
- Dureza: 37-41 HRc como soldadura
- Polaridad: DCEP (electrodo positivo)
- Diámetros: 3/32" y 1/8"
- Precaliente y mantenga temperatura de interpase a no menos de 150°C, el tratamiento pos-soldadura no debe exceder la temperatura de 600°C.
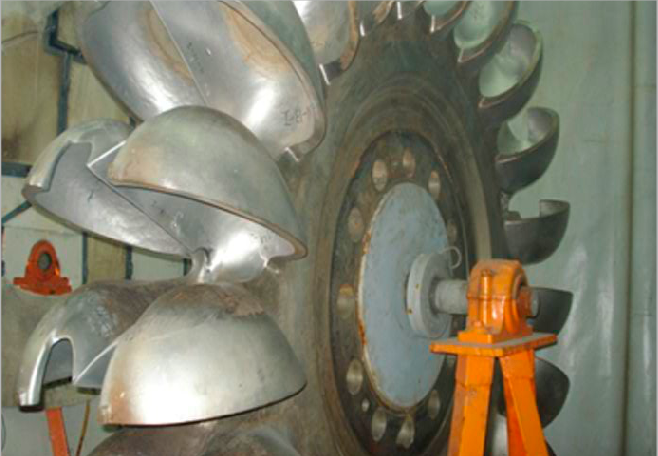
Comparación relativa de electrodos para aceros inoxidables de EUTECTIC+CASTOLIN
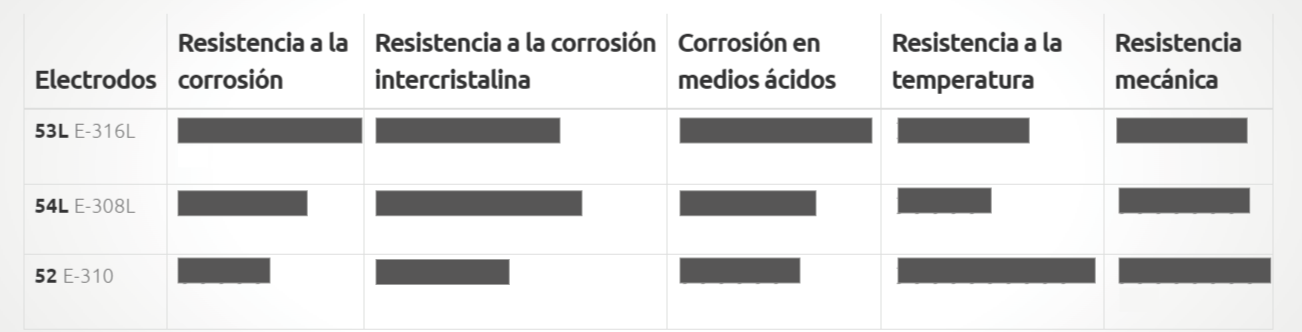