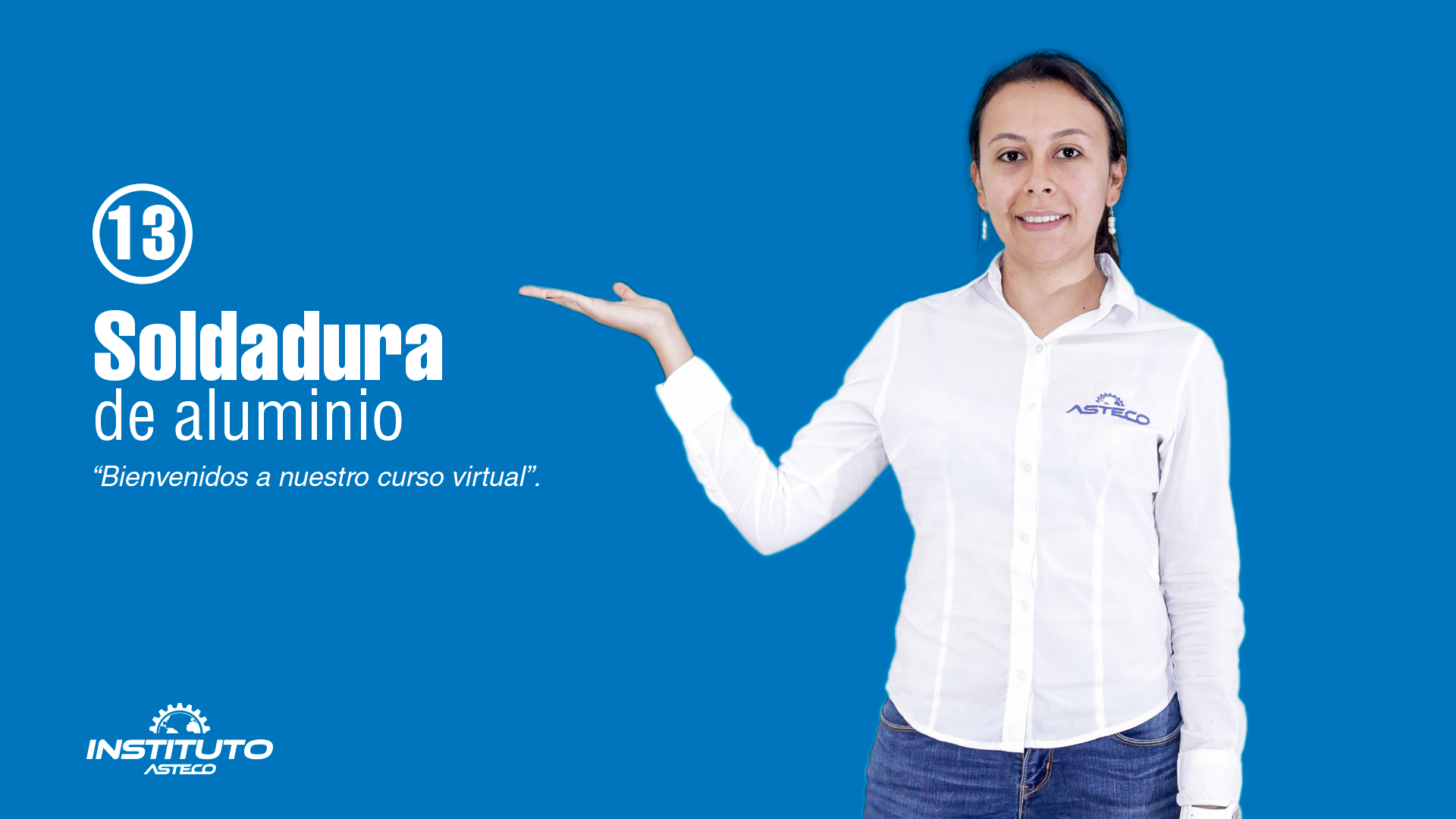
Propiedades
Muy liviano en peso y en algunas ocasiones puede tener una resistencia similar a la del acero de bajo carbono.
- Densidad: 2.7gr/cm2
- Alta resistencia a la corrosión.
- Alta ductilidad, aún en temperaturas bajo cero.
- No tóxico.
- Buena conductividad térmica y eléctrica.
- Buena reflectividad del calor y la luz.
- Temperatura de fusión del aluminio puro 660°C y de las aleaciones de aluminio es de 482 a 660°C.
- El óxido de aluminio funde a 2037°C
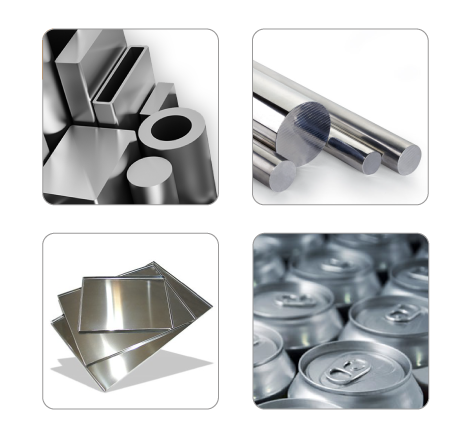
Generalidades AI
Las secciones muy delgadas podrían requerir precalentamiento. Para la soldadura de punto, los aluminios con alta conductividad térmica y eléctrica requieren corrientes más altas, tiempos de arco cortos y mayor control de las variables de soldadura que cuando se trata de una soldadura para un acero.
Tiene la capacidad de formar una capa de óxido que debe ser removida, la razón para ello es que esta capa puede ser muy delgada y puede causar baja mojabilidad y poco flujo del metal de aporte.
Para soldar el aluminio es necesario conocer su punto de fusión y su composición química.
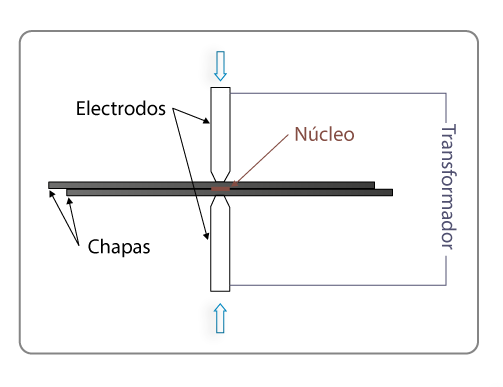
Microestructura AI
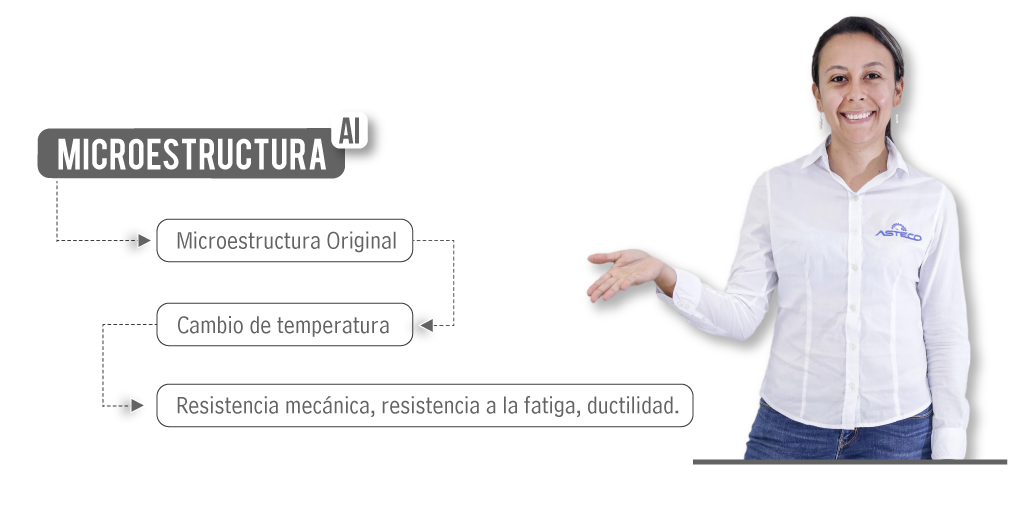
Clasificación de los aluminios forjados
99% Aluminio | 1XXX |
Cobre | 2XXX |
Manganeso | 3XXX |
Silicio | 4XXX |
Magnesio | 5XXX |
Magnesio y silicio | 6XXX |
Zinc | 37XXX |
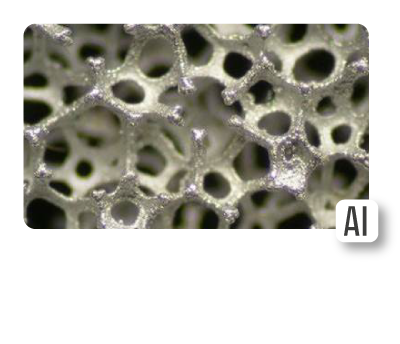
Aleaciones no tratables térmicamente
La resistencia inicial depende de elementos aleantes como Si, Fe, Mn y Mg.
Series 1XXX, 3XXX, 4XXX y 5XXX.
La resistencia de estos aluminios debe ser mejorada por endurecimiento por deformación o endurecimiento en frío.
Designación | Aplicación |
---|---|
1060 | Procesos químicos, tanques |
1100 | Decoración, arquitectura |
1350 | Cable de conducción eléctrica |
3003 | Alimentos, petróleo, química |
3004 | Hojas de metal con más resistencia que el 3003 |
5005 | Eléctrica y arquitectura |
5052 | Resistencia a la corrosión, tanques, botes. |
Aleaciones no tratables térmicamente - Soldabilidad
Aleación de aluminio | Oxiacetilénica | Arco con fundente | Arco con gas inerte | Brazing |
---|---|---|---|---|
1060 | A | A | A | A |
1100 | A | A | A | A |
1350 | A | A | A | A |
3003 | A | A | A | A |
3004 | B | A | A | B |
5005 | A | A | A | B |
5052 | A | A | A | C |
Aleaciones tratables térmicamente
La resistencia inicial depende de elementos aleantes como Cu, Mg, Zn, Si Series 2XXX, 6XXX y 7XXX.
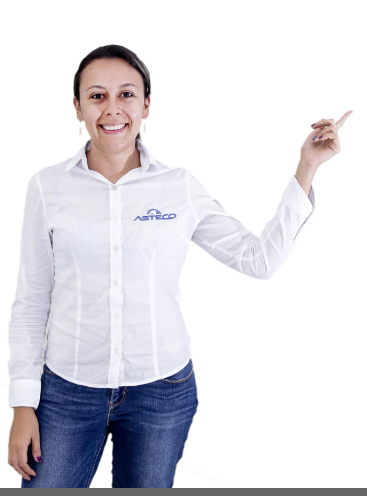
Designación | Aplicación |
---|---|
-0 (recocido) | Estabilidad dimensional, ductilidad |
-F (fabricación) | Conformación sin control de T |
-T1 | No hay trabajo en frío |
-T2 | Productos endurecidos en frío |
Aleaciones tratables térmicamente - Soldabilidad
Aleación de aluminio | Oxiacetilénica | Arco con fundente | Arco con gas inerte | Brazing |
---|---|---|---|---|
2014 | X | C | C | X |
2024 | X | C | C | X |
6010 | C | C | B | X |
6061 | A | A | A | A |
6063 | A | A | A | A |
7075 | X | X | C | X |
Selección del metal de aporte
- Libre de grietas.
- Resistencia a la tracción o al cizallamiento del metal de soldadura.
- Ductilidad de la soldadura.
- Temperatura de servicio.
- Resistencia a la corrosión.
- Coincidencia del color luego del anodizado.
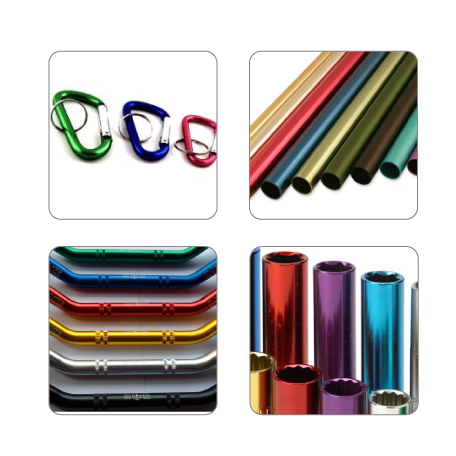
Aspectos a considerar
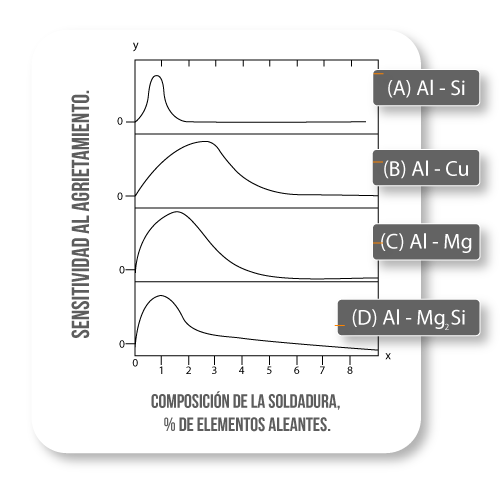
Generalmente, para los aluminios no tratables térmicamente, se usa un metal de aporte con la misma composición química del metal base.
Para los aluminios tratables térmicamente, se usa un aporte disímil que tenga una temperatura de fusión menor a la del metal base y una resistencia similar o menor.
Guía para la preparación de la superficie
La principal causa de porosidad en el aluminio es el hidrógeno. Esta humedad puede albergarse en la capa de óxido superficial, la cual es difícil de remover con el arco ya que funde a 2038°C (tres veces el punto de fusión del aluminio).
Se deben almacenar en un ambiente seco. No se debe almacenar una placa o pieza encima de otra.
Antes de soldar se debe remover la grasa, aceite, suciedad, pintura o elemento que pueda generar humedad o que pueda interferir el proceso de fusión de la soldadura.
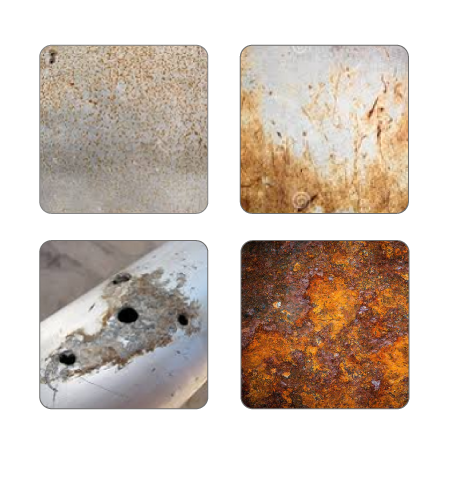
Aspectos a considerar
Tipo de solución | Concentración | Temperatura | Arco con gas inerte | Propósito |
---|---|---|---|---|
Soda cáustica y ácido nítrico | 1.76oz/gal de agua. HNO3 al 68% y agua. |
60 – 71°C | Inmersión de 10 a 60 s en la solución, 30 s en agua fría y 30 s en agua caliente. | Remover capa de óxido. |
Sulfuro crómico | H2SO4 (1gal) + CrO3 (45oz)+ agua(9gal) | 60 - 82°C | Inmersión 2 a 3 min. Agua fría/agua caliente. Secar | Remover TT y recocido. |
Ácido sulfúrico | H2SO4 (5.81oz) - agua (1L) | 73°C | Inmersión de 5 a 10 min. Agua fría/agua caliente. Secar | Remover óxido. |
Sulfato férrico | Fe2SO4 H2O 10% de volumen | 26.7°C | Inmersión de 5 a 10 min. Agua fría/agua caliente. Secar | Remover óxido. |
Aspectos a considerar
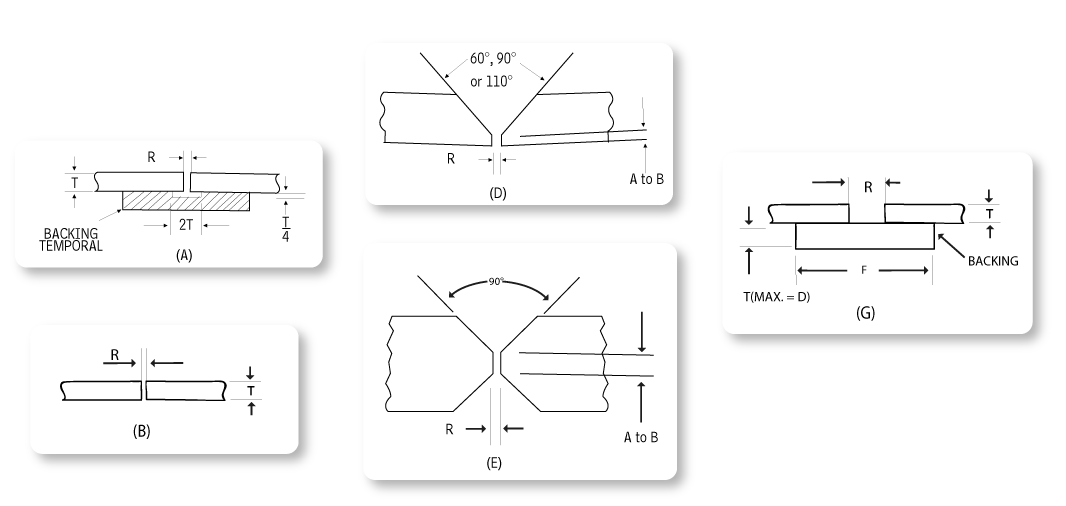

Proceso GTAW
- Usa un electrodo no consumible de tungsteno.
- Gas de protección: argón, helio o mezcla de ellos.
- Usualmente fuente de corriente constante.
- Corriente alterna o pulsada, generalmente con DCEN.
- La remoción del óxido se hará sólo cuando el electrodo es positivo, para ello el equipo debe 125V RMS para argón y 150V RMS para helio o alta frecuencia.
- La estabilidad del arco se relacionará con el sonido.
- Si hay más de 50% de helio la longitud del arco debe ser más corta.
- El arco debe iniciarse lejos del metal base y posteriormente se acerca el tungsteno y se inicia el arco en el material base.
- Longitud de arco aproximadamente igual al diámetro del electrodo de tungsteno.
- Puede aparecer una capa de óxido que debe ser removida y no puede confundirse con faltas de fusión.
- El helio dará mayor penetración que el argón.
- La soldadura DCEP permite soldar placas delgadas, se debe usar argón.
- La soldadura con corriente pulsada permite limpieza de la superficie asociada a la corriente alterna y buena penetración. Se pueden usar mezclas argón/helio.
Procesos - GTAW - gases de protección
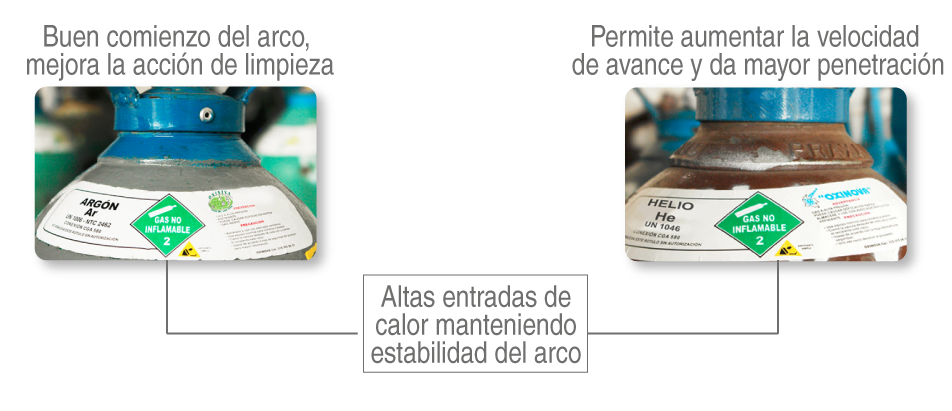
Procesos - GMAW
Se debe seleccionar un adecuado sistema de alimentación del electrodo (push, pull o push pull).
Se pueden usar fuentes de corriente o voltaje constante pero las más recomendadas son las de voltaje constante.
Transferencia por aspersión o si es intermitente se conoce como aspersión pulsada.
Para este proceso se debe considerar: diámetro del electrodo, velocidad de alimentación del alambre, gas de protección, tasa del pulso, voltaje pico del pulso, corriente promedio, velocidad de avance.
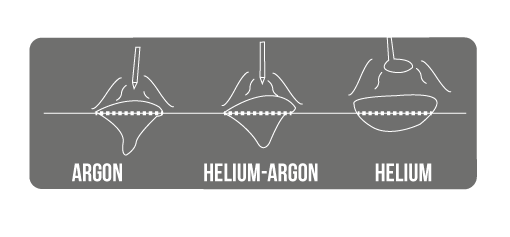
Procesos - SMAW
- La velocidad de soldadura es menor.
- No se recomienda cuando se requiere una buena calidad, acabado y desempeño de la junta soldada.
- Se debe realizar una muy buena remoción de la escoria porque puede generar oxidación. Los electrodos deben ser precalentados antes de usarse.
- Se debe considerar: los aleantes presentes en el revestimiento del electrodo, la limpieza del material base y del electrodo, el precalentamiento del metal base y una adecuada remoción de la escoria.
- Se recomienda para espesores superiores a los 3 mm
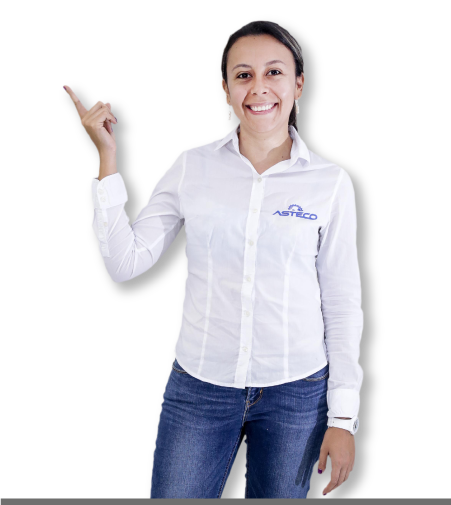
Brazing
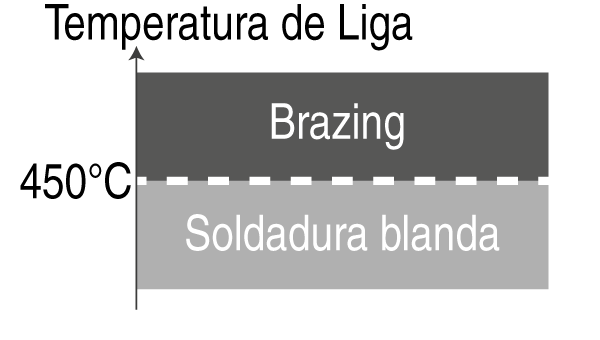
Para la selección del material de aporte se debe tener en cuenta: fluidez, resistencia mecánica, resistencia a la corrosión y elongación.
- Soldadura por capilaridad.
- Requiere excelente limpieza de la pieza.
- Diseño adecuado de la pieza para permitir la capilaridad.
- Permite soldar espesores muy pequeños.
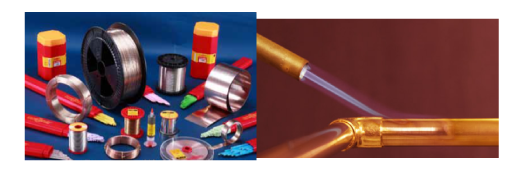